Innovation at MADE: Carbon Fenders and Titanium Forks
Last weekend, the MADE Show in Portland celebrated the art of framebuilding, as the show’s official motto put it. Of course, the exhibitors brought much more than just beautifully crafted and gorgeously painted frames. There was some real innovation, as well as other news that didn’t make it into the more mainstream reports from the show. Here are a few things Natsuko and I noticed at the show.
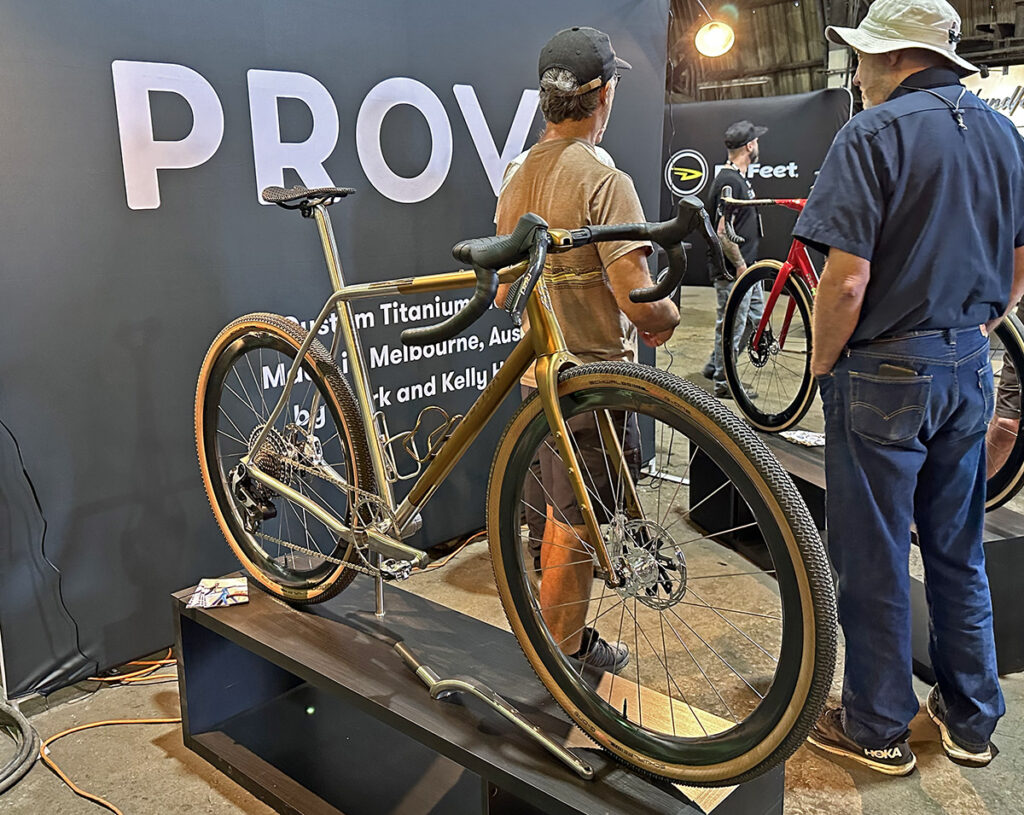
Perhaps the biggest tour de force was on display at the Prova stand: a 3D-printed titanium fork. According to the Australian builder, the new titanium fork offers more compliance than a carbon fork, without a weight penalty.
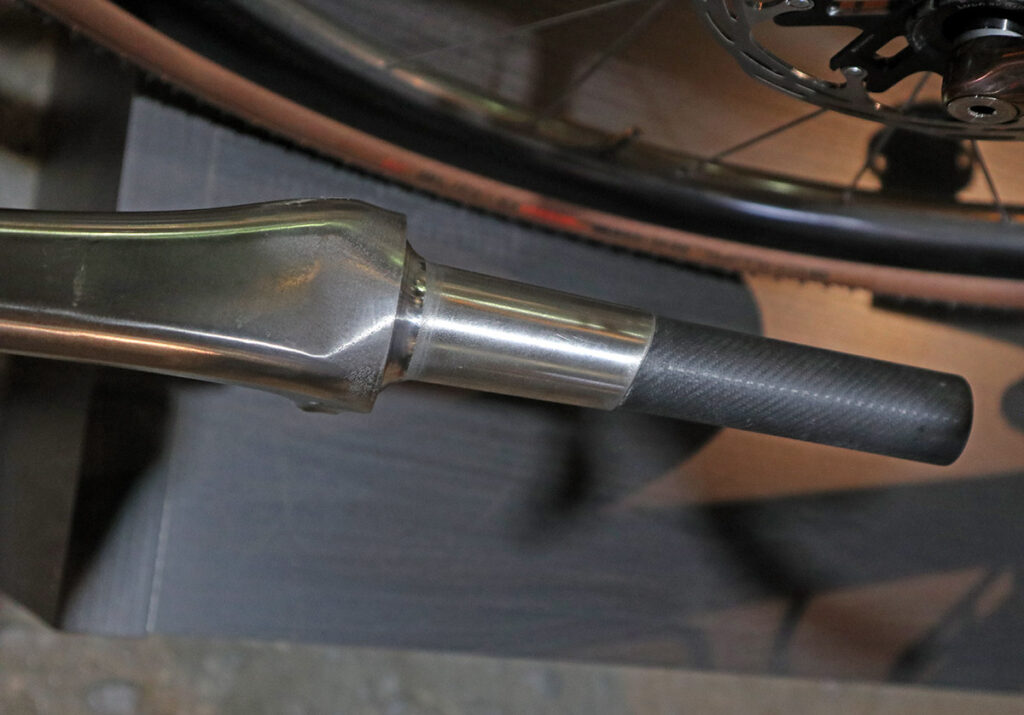
The fork crown, upper half of the blades and lower half of the steerer are 3D-printed in one piece from titanium. The top of the steerer is made from carbon. The lower fork blades appear to be made from titanium tubing and welded onto the upper halves.
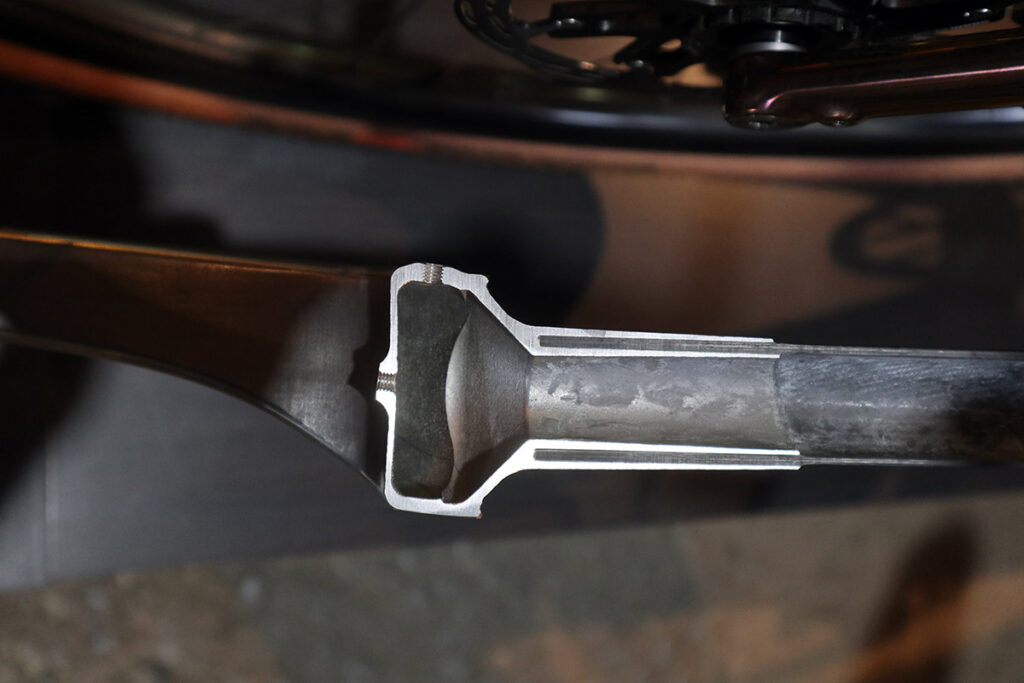
A sectioned fork showed how the carbon steerer fits in between the double-walled lower titanium steerer. The bearing seat for the headset is visible on the inside, showing off the minimalist design: There is no more material than absolutely necessary on this fork. Threaded holes allow for fender and rack mounting. It’s a remarkable piece of engineering, made possible by 3D printing. The new fork won’t be available separately, but only as an upgrade on Prova titanium frames. The cost? As they say: “If you have to ask…” I forgot the exact number, but it was several thousand dollars for the fork alone.
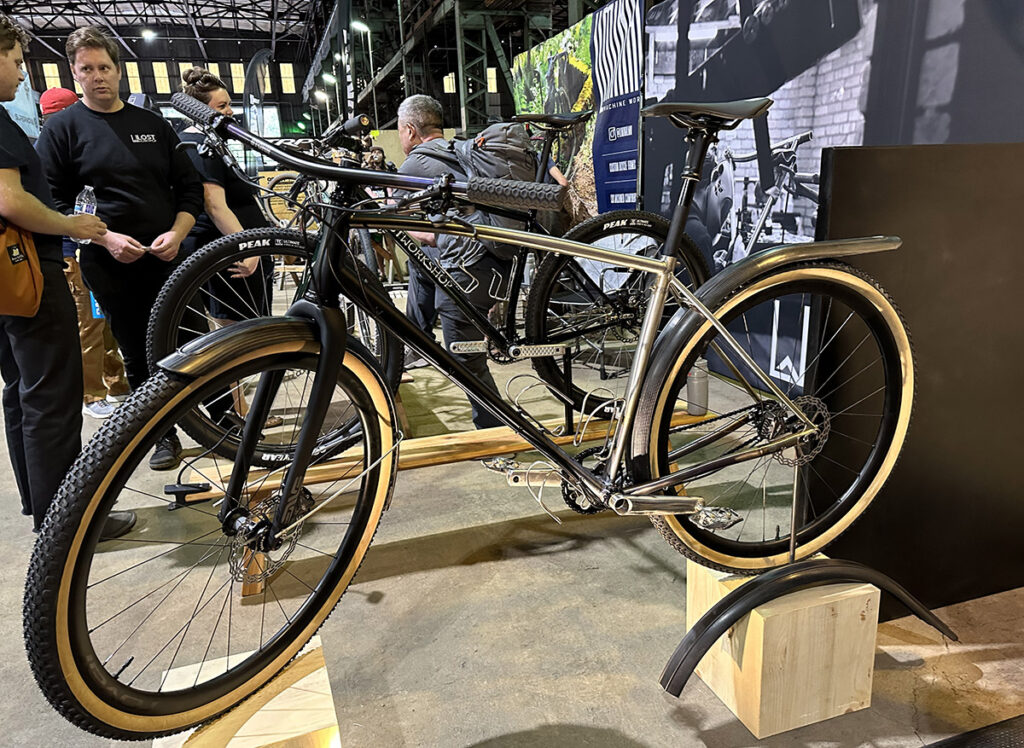
Over at Btchn bikes, Tyler Reiswig showed the latest, production-ready iteration of his carbon fenders. “It’s taken several years to get them just right,” Tyler told us. Now they follow the curve of the tire beautifully. Tyler is especially proud that the fenders now incorporate a gutter similar to the rolled edge of aluminum fenders to prevent water from dripping off the fender edge. It’s a reminder that there have been carbon fenders before, but none that offered the same functionality as the best aluminum fenders.
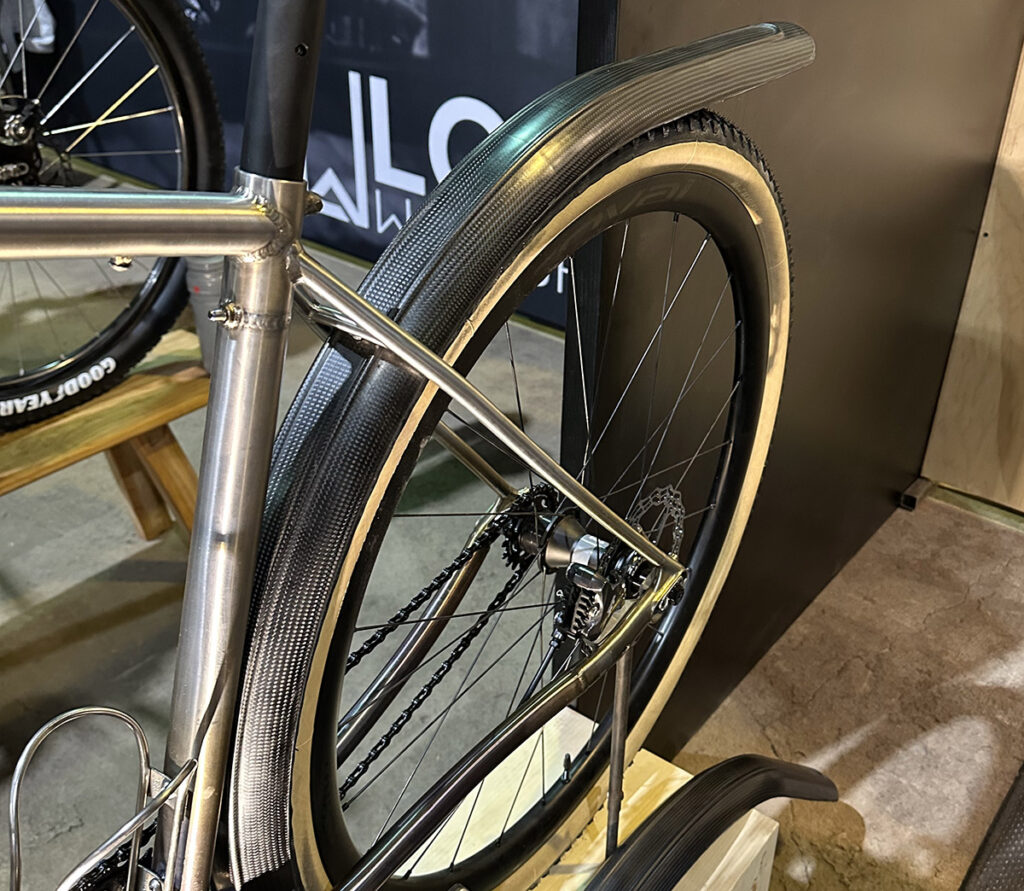
The rear fender is designed to be mounted without stays. “Your friends may not like you as much,” Tyler joked, since the rear fender is designed to protect only the rider, not those who follow behind.
Two hollow reinforcement channels make it stiff enough so it doesn’t wobble. The channels are created by inserting silicone beads into the layout. Once the carbon has cured, the silicone is removed.
The front fender does use a tubular Rene Herse fender stay and relies on the carbon fork to stabilize it further. Beautifully made and devilishly difficult to manufacture, these fenders also won’t come cheaply. Tyler told me the manufacturing cost alone is several time the price of a set of top-end aluminum fenders.
Another Btchn displayed a novel system to adjust the seat angle. Tyler explained: “We ride our bikes to the trails, but the 78° seat angle means that those miles are no fun at all. Yet the steep seat angle is necessary for ultra-steep climbs. So we figured why not make the seat tube adjustable so it works great on all terrains.”
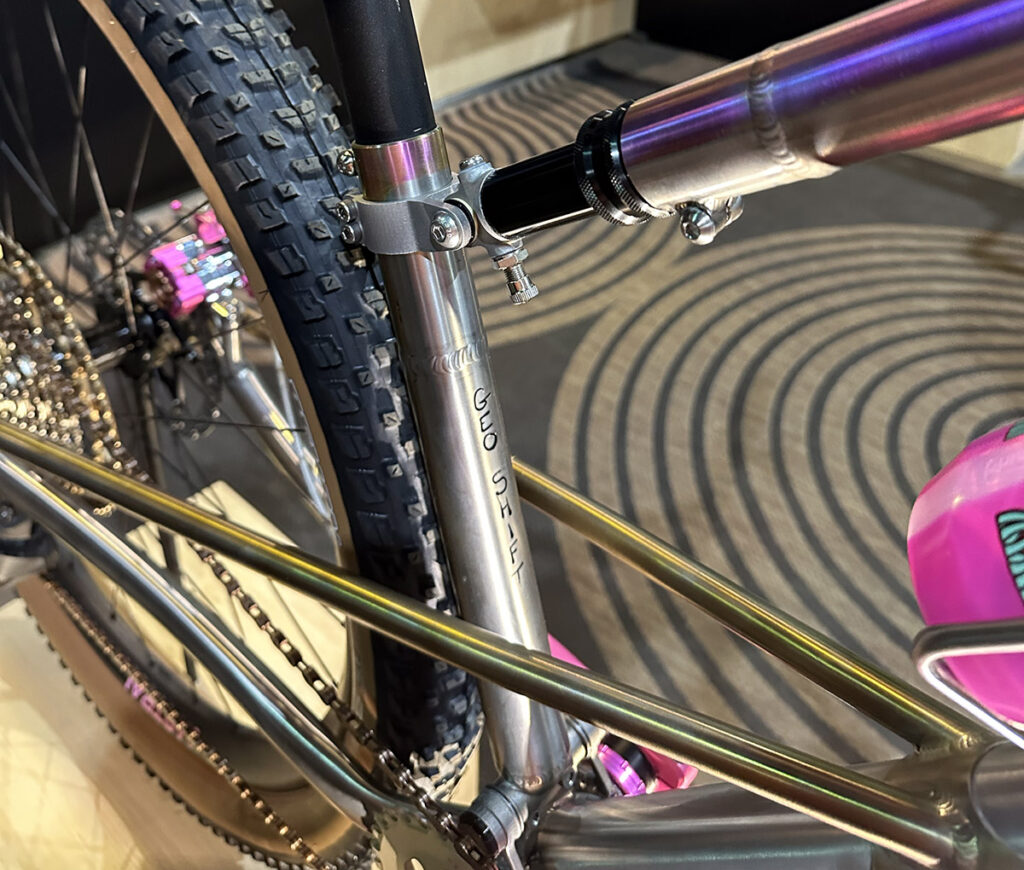
Using a system similar to a dropper seatpost, the seat angle can be slackened for riding on flat terrain, and steepened for technical climbs. It’s nice to see a builder thinking outside the box and coming up with new ideas.
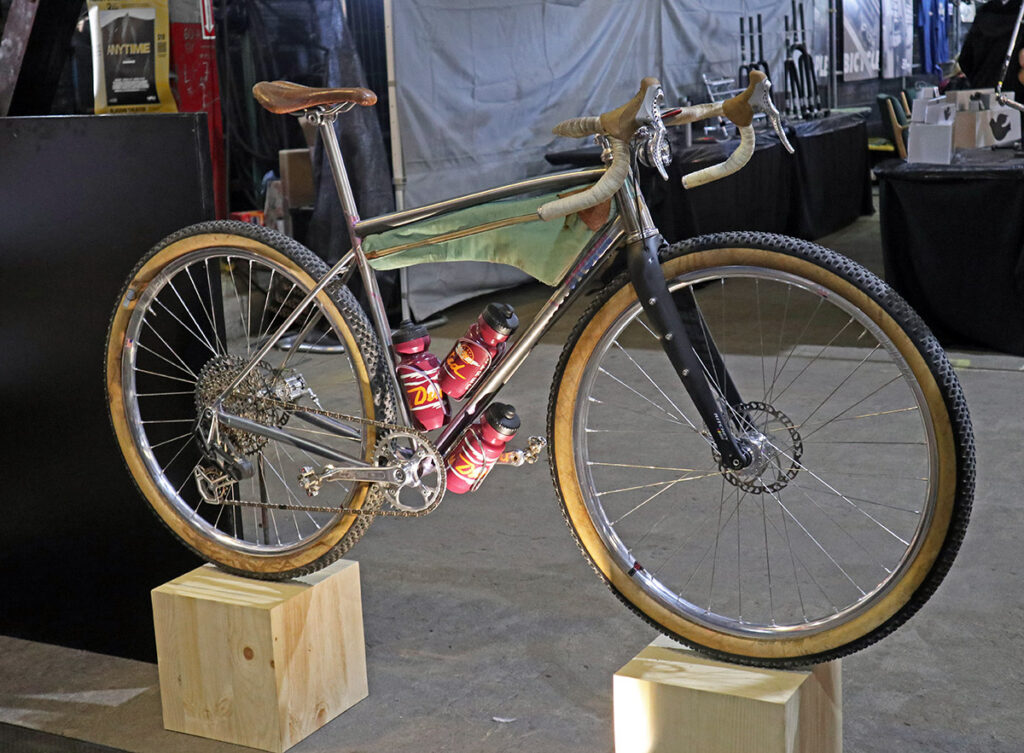
Looking at the bikes on display, I was often drawn to the personal bikes of the builders. Tyler’s own Btchn titanium bike had the patina of much use, plus some innovative features. The electronic shifter is controlled by micro-switches that are hidden under the rubber hoods of the old-school brake levers. This is a bike I’d like to try!
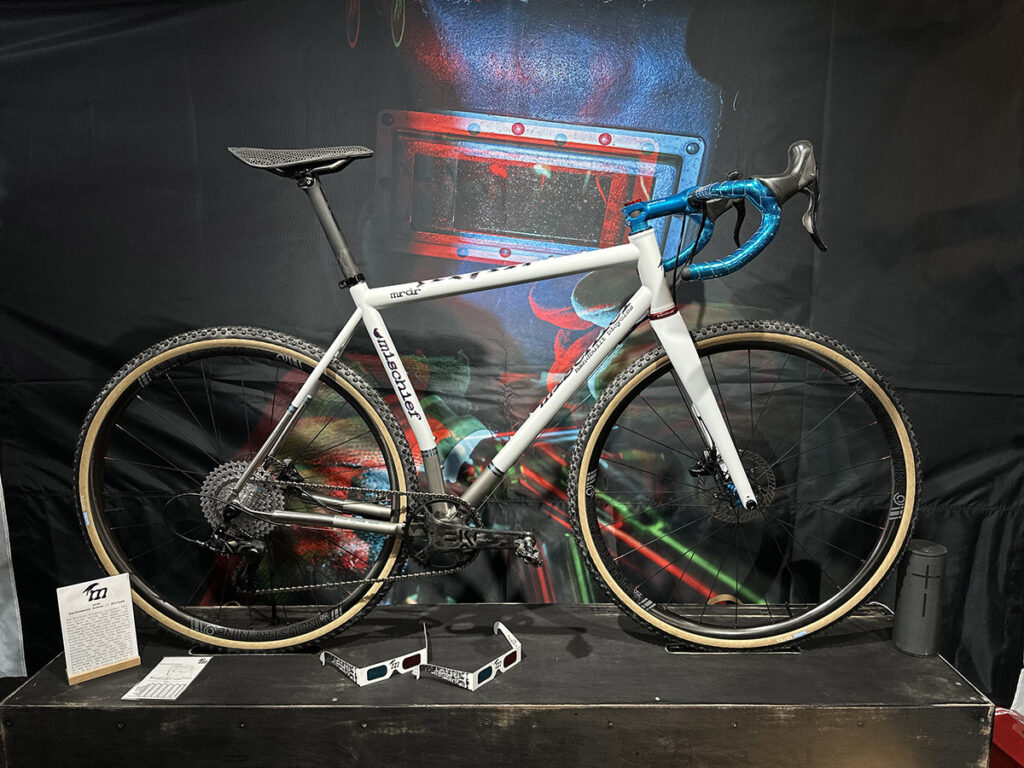
Another bike that looked like it would be fun was Chris Wahl’s personal machine. When famous Seattle builder Bill Davidson retired, Chris took over the shop and added his own Mischief line to the program. What the photo can’t show are the 3D logos, visible with the glasses you see in the foreground. Because why not? More seriously, the titanium frame is as light as most carbon frames, to create bike that performs equally well on pavement and gravel.
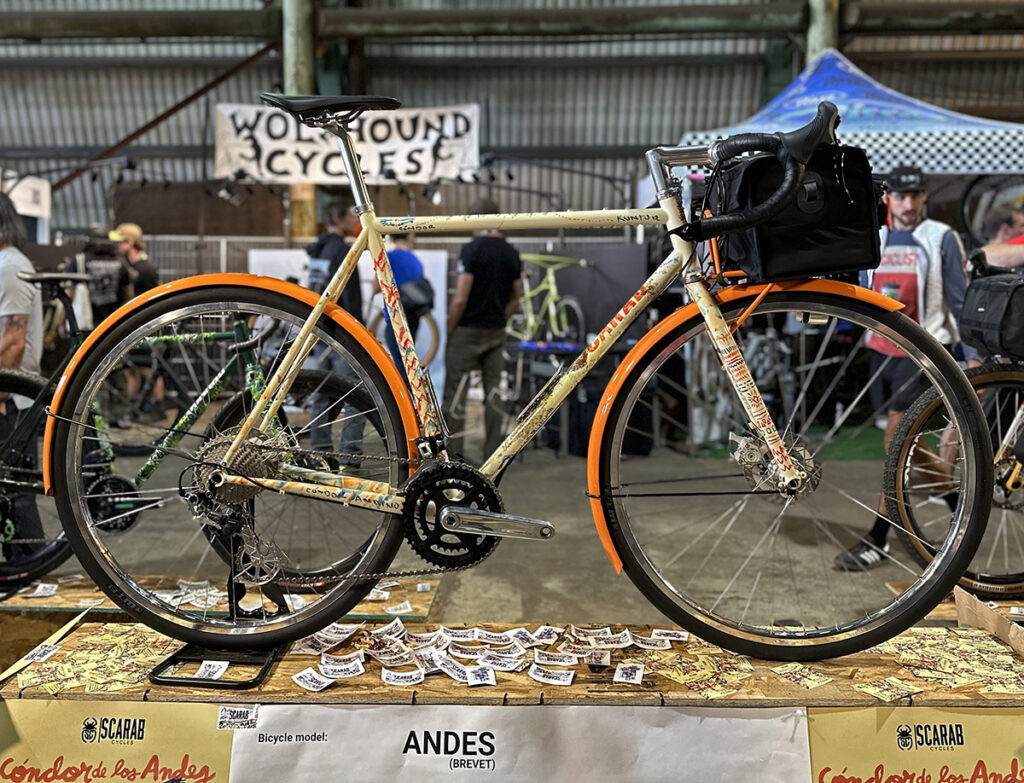
A number of builders showed their first efforts at making fully-equipped randonneur bikes—here is Scarab’s new Andes model. It’s exciting to see fully equipped bikes that are intended for long and spirited rides.
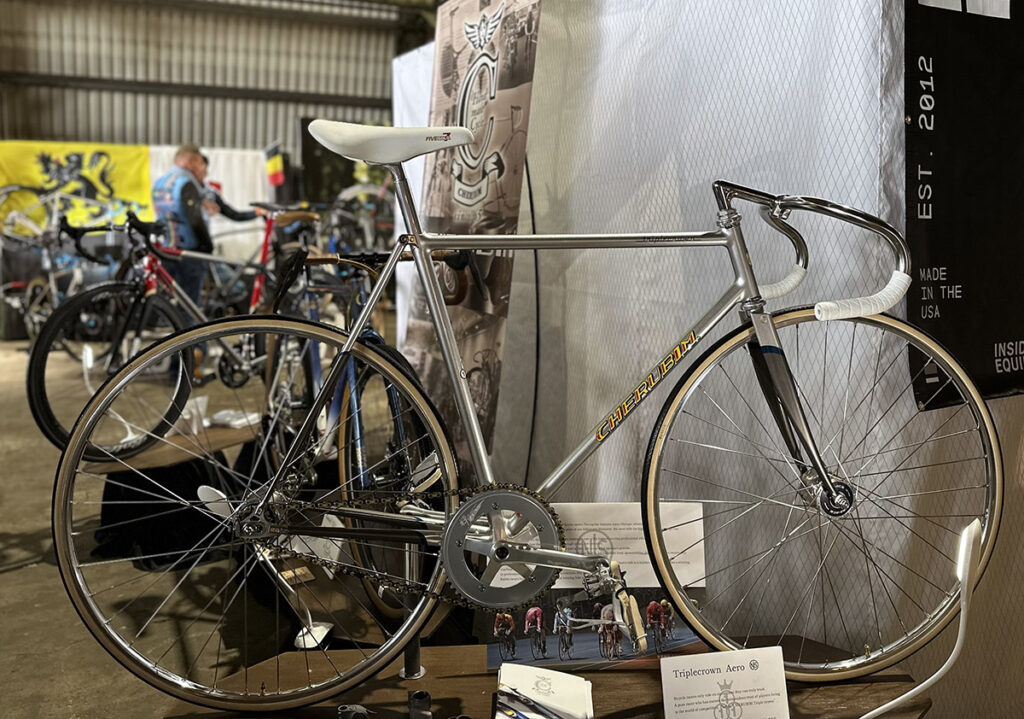
Cherubim had come all the way from Japan to display their beautifully crafted machines. Their track bike probably deserved the award for the narrowest tires. (They also had a road and a gravel bike on display.)
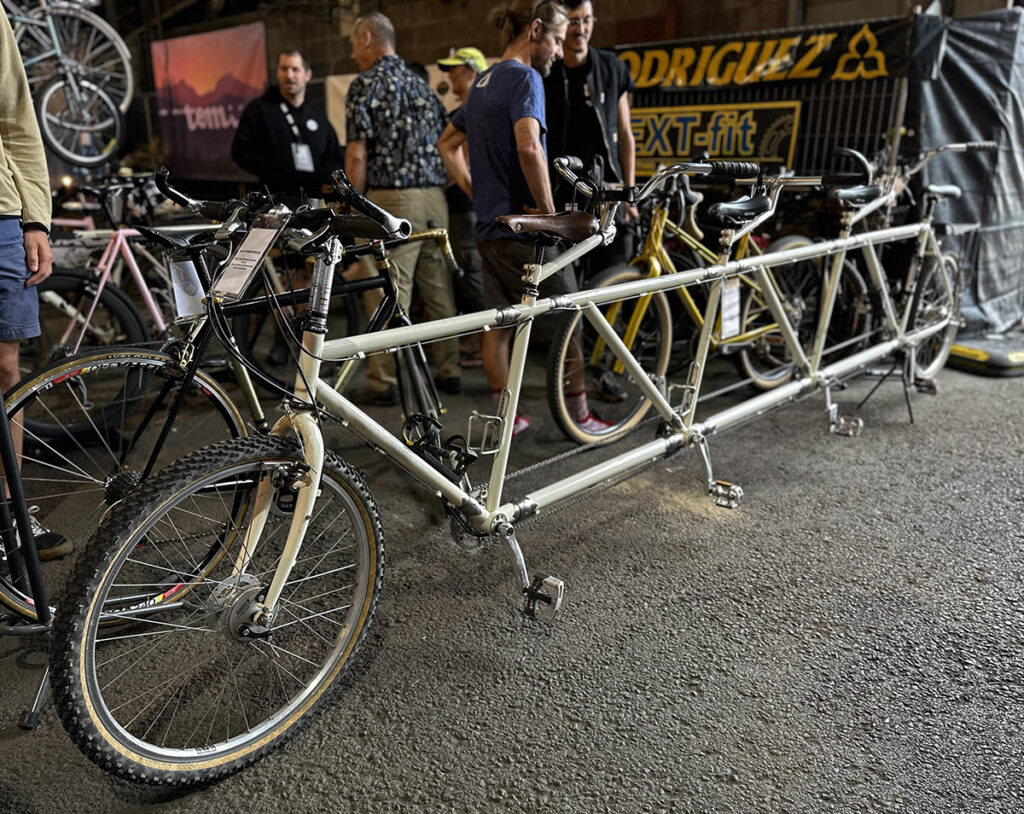
Seattle builder Rodriguez, now in the hands of a young and enthusiastic crew, displayed a range of well-used bikes to highlight that their bikes are meant to be ridden. Their quintuplet was by far the longest bike at the show. The modular frame uses couplers, so it can be adapted for any number of riders, between one and five. All cables also have couplers, and the lengths are carefully measured, so no adjustments of brakes or derailleurs are needed when a section is added or removed.
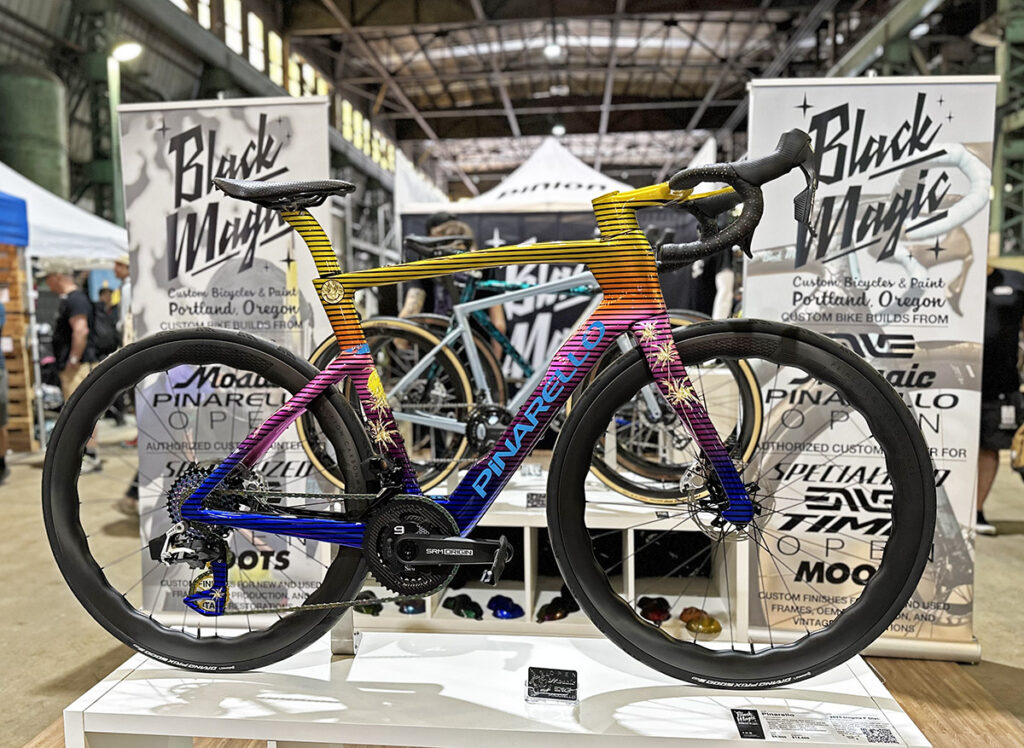
Black Magic showed amazing custom paint on production frames. The paint job on this Pinarello reportedly took 100 hours to create. They are true masters of their craft, and it shows.
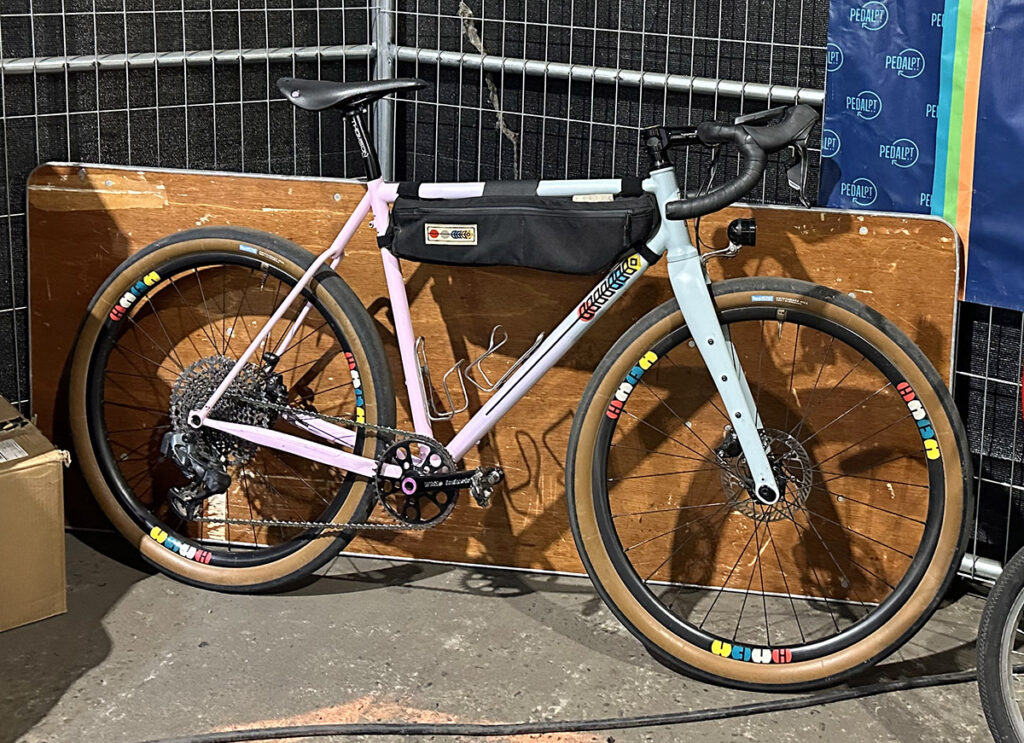
In addition to the bikes on display, we really enjoyed seeing the bikes of visitors and volunteers that were parked around the show. It was a reminder that all the bikes at the show are intended to be ridden and enjoyed.
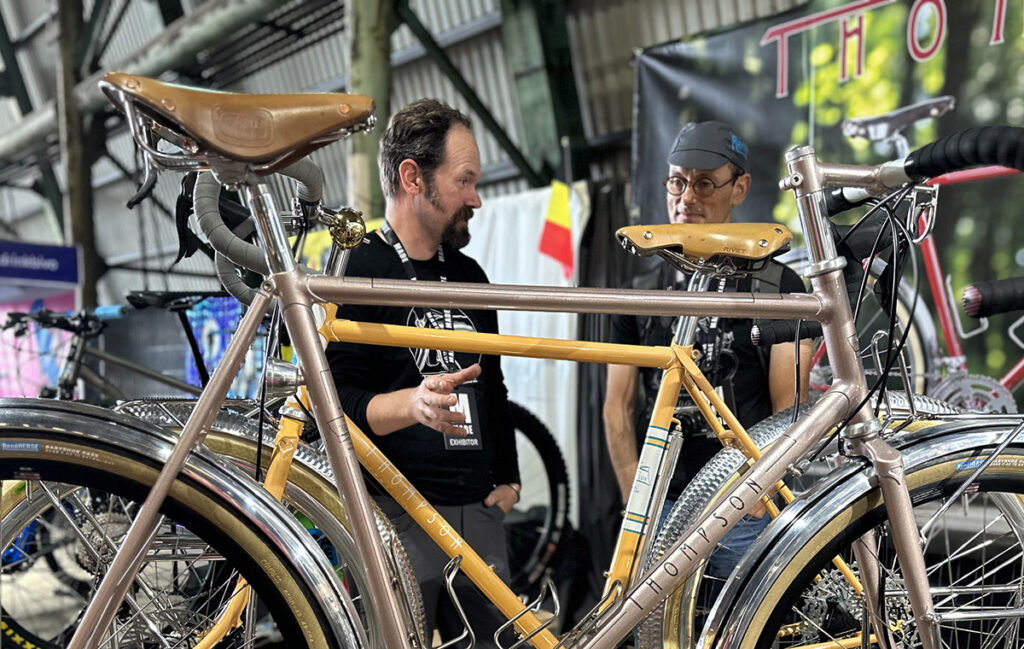
Most of all, it was great fun to talk to the builders and visitors, exchanging impressions and discussing new ideas—above with Corey Thompson, who brought a brace of his tried-and-true rando bikes to the show. And we’re also grateful to see so many builders chose Rene Herse tires and parts for their bikes. We don’t offer free tires for show bikes, so all these builders bought these tires because they think our supple high-performance tires best complement the performance of their bikes.
A big thanks to Billy Sinkford and his crew for organizing such a wonderful event.